“DEDICATION TO QUALITY” AT MASS PRECISION
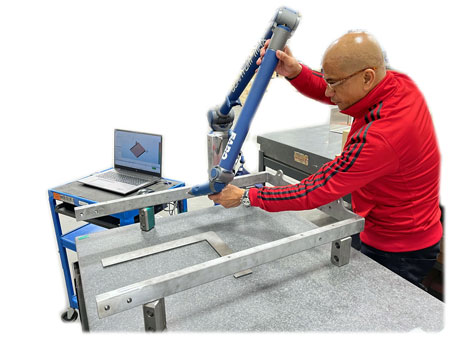
SATISFYING THE CUSTOMER BY MEETING OR EXCEEDING EXPECTATIONS THROUGH CONTINUOUS IMPROVEMENT AND MEETING REGULATORY REQUIREMENTS
In 1993, MASS Precision became one of the first Design and Manufacturing company on the West Coast to be Certified to I.S. EN ISO 9001:2015. State of the art inspection equipment and methodology combine to provide the customer with the assurance that their products will meet specification. Coordinate measuring machines, both contact and optical, are used to capture SPC data and process capability analysis.
MASS is certified to I.S. EN ISO 13485:2016 (ISO Standard Quality Management System for the design and manufacture of medical devices). Scope: Contract Design, Manufacturing, System Integration and Testing of Metal Components, Assemblies and Electro-Mechanical Assemblies for (Non-Sterile) Medical Applications
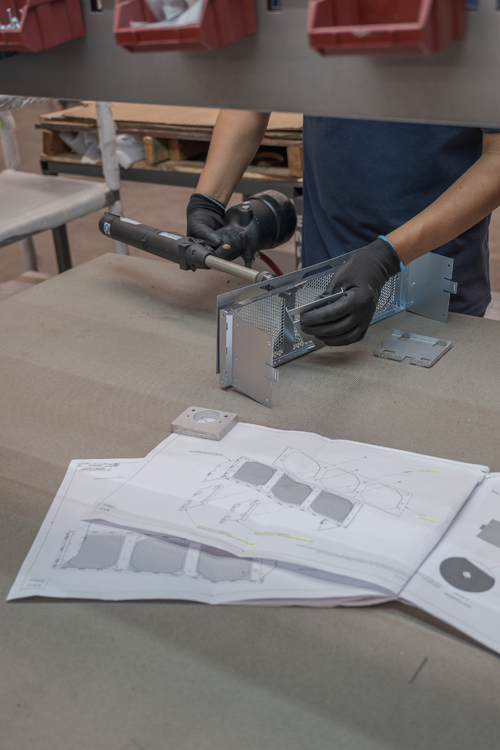
MASS PRECISION EMBODIES “COMMITMENT TO QUALITY”
QUALITY PLANNING
At MASS Precision, our commitment to quality is evident in our meticulous planning. As one of the pioneering Design and Manufacturing companies certified to I.S. EN ISO 9001:2015 on the West Coast since 1993, we employ state-of-the-art inspection equipment and methodology to assure customers that their products meet specifications. The use of coordinate measuring machines, both contact and optical, aids in capturing Statistical Process Control (SPC) data and conducting process capability analysis.
Additionally, MASS holds certification to I.S. EN ISO 13485:2016, emphasizing our adherence to the ISO Standard Quality Management System for the design and manufacture of medical devices. Our scope includes Contract Design, Manufacturing, System Integration, and Testing of Metal Components, Assemblies, and Electro-Mechanical Assemblies for (Non-Sterile) Medical Applications.
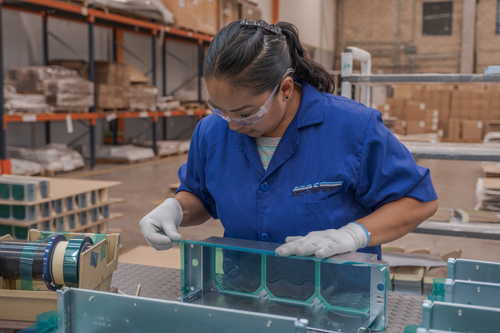
CONTINUOUS IMPROVEMENT
MASS invests in a comprehensive training program, providing employees with opportunities to enhance skills across all business processes. Continuous improvement is ingrained in our culture, challenging standard practices and workmanship standards for relevance and effectiveness. The Senior Quality Team, comprising senior management, sets and achieves goals, pushing for excellence.
Objectives are clearly defined, measured, and analyzed, with progress acknowledged. Self-directed work teams play a vital role in goal setting, measurement, analysis, and reporting of results. Our Corporate Training program, administered and assessed by Human Resources, ensures that all MASS employees actively participate in continuous upgrades to skills and roles.
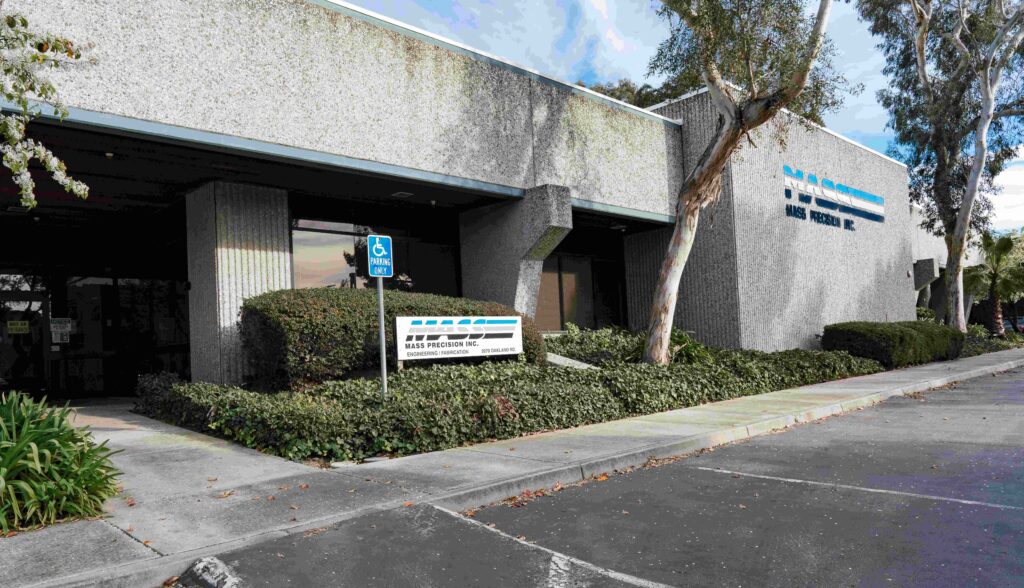
CUSTOMER SATISFACTION
Customer Satisfaction is the cornerstone of our growth strategy, aiming for new opportunities and sustained growth. We value customer feedback as the voice of the customer, providing insights to better understand expectations and enhance customer relations.
Customer feedback, the voice of the customer, is shared with management to better understand expectations and continue to improve customer relations.
Formal Management Review meetings occur monthly, maintaining a focus on customer satisfaction. These reviews cover feedback from surveys, feedback reports, quote capture rates, and more. Issues and actions related to specifications, lead-times, system capabilities, Defects Per Part Million (DPPM) expectations, and responsiveness are thoroughly addressed.
Current Certifications and Registrations:
I.S. EN ISO 9001:2015 San Jose, Mexico, Malaysia
I.S. EN ISO 13485:2016 Fremont
Fremont Facility Registered with FDA
Medical Devices listed with FDA
UL Registered
ITAR Registered
Copies available upon request
Equipment List Available Upon Request